Material testing is a critical process in various industries including manufacturing, automotive construction, and aerospace it involves evaluating materials to determine their properties and performance under various conditions. This testing can include mechanical, chemical, and physical assessments to ensure that materials meet the necessary standards for safety, durability, and functionality.
Key Reasons for Material Testing:
- Safety and Compliance: Ensuring materials meet regulatory standards to prevent failures that could lead to accidents or product recalls.
- Quality Assurance: Verifying that materials possess the required properties for their intended use, which helps in maintaining consistent product quality.
- Performance Evaluation: Assessing how materials behave under different stresses and conditions to predict their performance in real-world applications.
- Cost Efficiency: Identifying the most suitable materials for a specific application can reduce costs by avoiding over-engineering and ensuring longevity.
- Innovation: Supporting the development of new materials and technologies by understanding material properties and limitations.
- Environmental Compliance: OEMs that manufacture products subject to environmental regulations may want to know the exact chemical composition of their goods. In these instances, product testing can ensure that the regulated chemicals their items contain are below certain thresholds, and the commodity itself is legally compliant.
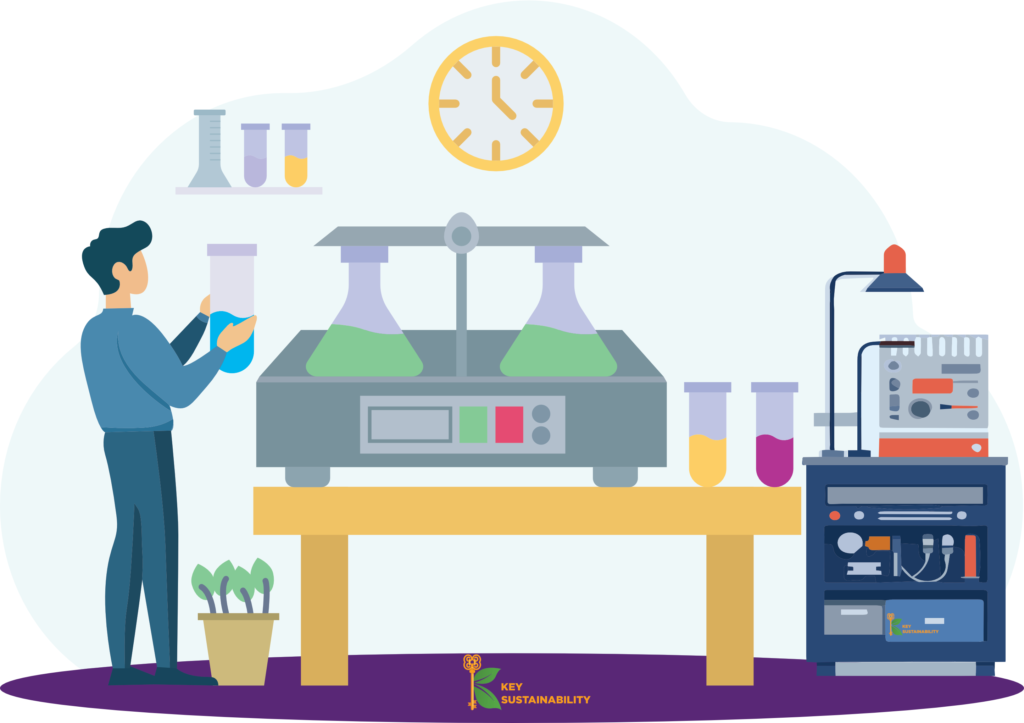
Production Part Approval Process (PPAP)
The Production Part Approval Process (PPAP) is a standardized procedure used in manufacturing to ensure that suppliers can consistently produce parts that meet all customer specifications and quality requirements. Initially developed by the automotive industry, PPAP is now widely used across various sectors.
Importance of PPAP:
- Supplier Validation: Confirms that suppliers understand and can meet the customer’s engineering design specifications.
- Quality Assurance: Ensures that the production process is capable of consistently producing parts that meet quality standards.
- Risk Mitigation: Identifies potential issues in the production process before full-scale manufacturing begins, reducing the risk of defects and failures.
- Documentation and Traceability: Provides comprehensive documentation that can be used for future reference and traceability.
Key Elements of PPAP:
- Design Documentation: Includes drawings and specifications to ensure the correct part is being produced.
- Engineering Change Documentation: Tracks any changes to the design or process.
- Process Flow Diagram: Outlines the entire manufacturing process.
- Process Failure Mode and Effects Analysis (PFMEA): Identifies potential process failures and their impacts.
- Control Plan: Details how each part of the process will be controlled to maintain quality.
- Measurement System Analysis (MSA): Evaluates the accuracy and reliability of measurement systems.
- Dimensional Results: Verifies that parts meet specified dimensions.
- Material and Performance Testing: Ensures materials meet required standards.
By integrating material testing and PPAP, manufacturers can achieve higher levels of quality and reliability, ensuring that products are safe, compliant, and fit for purpose. This combination is essential for maintaining competitive advantage and customer satisfaction.
Do contact us for more information and to tackle the supply chain to comply for the regulations from start to finish.
+91-9740000662|shridhar@keysustainability.com